A close look at SimRefinery 
Two nights ago, a reader on the tech news site Ars Technica named postbebop uploaded a copy of SimRefinery to the Internet Archive. This is incredibly exciting news, and it’s given us our first chance to take a closer look at the game. SimRefinery was not fully completed by Maxis, and we can learn a lot about the game from the state it was left in. Based on my research, I want to add some context and explain what some of the peculiarities the game might say about its development.
Additionally, science journalist Maddie Stone got in touch with another former Chevron engineer, who provided a copy of the game’s “Tour Book,” as well as a guide document by Maxis Business Simulations and an academic article from UC Davis and Chevron about the educational use of SimRefinery.
Between the game and these new documents, we have a lot more we can learn about SimRefinery! Let’s take a look.
SimRefinery was developed for the Chevron oil company by Maxis Business Simulations, a short-lived division of SimCity developer Maxis that specialized in making games for corporations and government organizations. If you haven’t already, please read my article about the history of Maxis Business Simulations. I’ll frequently reference this article as we explore the game. Over the next few days, I’ll be updating the original article with some of the new information discussed here.
If you want to follow along, you can play SimRefinery in your browser on the Internet Archive! Once the game finishes installing, type “intro” to watch the tutorial or “simref” to start the game. (Note: This copy of the game is currently offline.)
According to press reports at the time, SimRefinery was only ever completed as a prototype, and this copy of SimRefinery confirms it. The game is largely unfinished. In multiple places, it even explicitly says that it is an incomplete prototype. Based on the Tour Book distributed with the game, this was also the version of SimRefinery that was tested internally in Chevron training courses. The Tour Book includes an evaluation section at the end asking Chevron employees for their feedback and suggestions.
There might be a question about whether this is an earlier version of the game, but as far as I can tell, this was the last version of SimRefinery that was delivered to Chevron. The SimRefinery prototype was made for a surprisingly low budget of $75,000, and it’s understandably missing features that a higher-budget game might have. It was meant to be expanded on if Chevron wanted to continue the project, but it was never adopted within the company and development didn’t go any further.
In a photo published in the San Francisco Chronicle in March 1993 – several months after the prototype was completed in October 1992 – you can see a little bit of barely legible text on the computer screen. It lines up with the text in the prototype that says “Game Prototype Presented by Chevron and Maxis.” If that was the version they were showing to the press half a year later, that leads me to believe that Maxis did not continue development past this point.
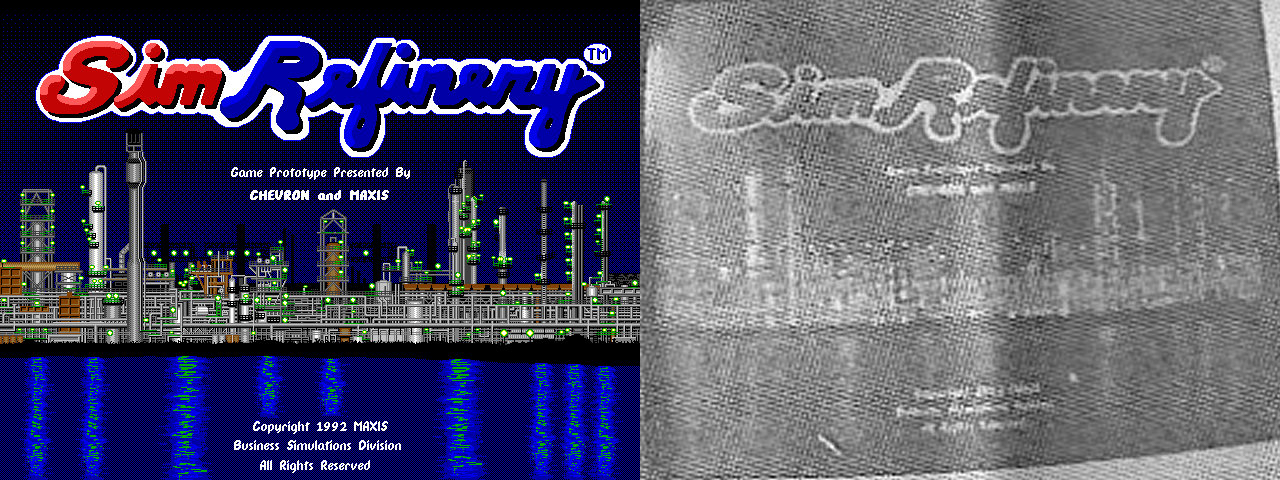
The final version of SimRefinery that Maxis showed off to the press in 1993 (right) was a prototype they created for Chevron. Development did not continue.
It’s possible that Chevron kept working on SimRefinery on their own, without the involvement of Maxis. In a presentation given in 1994 at the Foundations of Computer-Aided Process Design conference – two years after the prototype was completed – representatives from UC Davis and Chevron said they were “actively trying to bring together the right combination of people to further develop SimRefinery.” That would explain why Bruce Skidmore said he was asked to continue working on the game as late as 1998. However, this copy of SimRefinery is what Maxis Business Simulations was able to complete.
SimRefinery is split into two sections, a Map screen where you can examine the operation of the refinery, and an Edit screen that lets you build and customize the refinery. Most of the Edit screen doesn’t actually work; almost every button is a placeholder, but it appears that it would have given you tools similar to SimCity, like building roads and bulldozing. You can build more refinery plants, but they don’t seem to connect to anything. One of the only buttons that works is the Inspection button, which looks like a Chevron-branded hardhat, but the Inspection screen is mostly blank.
These placeholders were a way to indicate potential new features to the managers at Chevron. The Tour Book for SimRefinery says that the placeholders were meant to “suggest capabilities the simulation might include” and generate interest. In an article in Forbes, Esther Dyson suggested that SimRefinery would be expanded to simulate other refineries if it was successful, and these editing tools would likely have been part of that next phase of development that never came to fruition. But that tells us what the first priority was for SimRefinery – exploring the cause-and-effect at the refinery rather than customizing it, which is how Maxis Business Simulations tended to design their games.
Not much in SimRefinery is very polished, and it didn’t need to be, because this was a prototype for a corporate training tool. The interfaces are flat and rudimentary, and the game is full of typos and awkward language, like a drop-down menu with choices for “Load Old” and “Load New.” (Presumably, that meant “Load game” and “New game.”) SimRefinery was, after all, designed by a team of software engineers who had previously worked on programming infrastructure. This was their first game, and they were probably still adjusting to Maxis’s standards for user experience and presentation.
The games by Maxis Business Simulations were powered by the Whiteboard engine, a custom patchwork system that allowed the studio to put their simulations inside a graphical interface. The MBS team hadn’t worked with graphics like this before, and according to Bruce Skidmore, the lead engineer for SimRefinery, Maxis helped out by giving them “the guts of another game […] so we could learn how to manipulate the graphics on the screen.” I assumed the game they used was SimCity, but now that we can see SimRefinery up-close, it actually seems to be based on the 1993 game SimFarm!
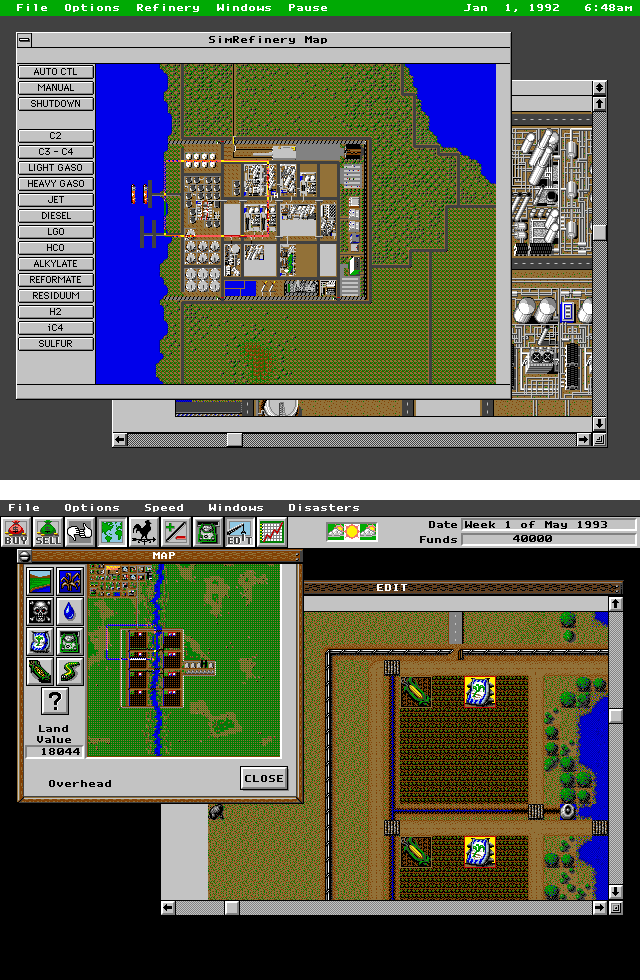
SimRefinery and SimFarm for DOS have the same general interface, including the same fonts, map interface, and the separate Map and Edit screens.
The interfaces of SimRefinery and SimFarm have so much in common. They even use the same font. You can see how the Whiteboard interface continued to evolve across each game by Maxis Business Simulations, with some elements carrying over to SimHealth and continuing to change in Project Challenge. This first version of the Whiteboard engine adds a recording tool, which captures mouse playback and allows you to record demos, and it seems to be identical to the recording tool used in SimHealth a year later.
The game comes with a pre-made tutorial recording of somebody from the development team playing SimRefinery. It feels like a surprising personal connection to watch someone play SimRefinery from 28 years ago.
Using SimFarm as a base is especially interesting because SimFarm was still in development when the SimRefinery prototype was completed. The team at Maxis Business Simulations probably had an early version of the game to work with. Unfortunately, there’s no credits listed in the game – that’s understandable since this wasn’t a commercial product – but it would have been interesting to see who else had worked on this game from the main Maxis office in Orinda, CA.
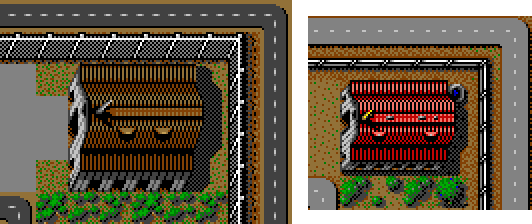
Some of the graphics in SimRefinery (left) are very similar to SimFarm. I set up the scene in SimFarm to look as close to the SimRefinery barn as possible for the sake of comparison.
The other fascinating thing is that many of the graphics in SimRefinery are lifted from SimCity and SimFarm. The game has plenty of original graphics for each of the refinery plants and endearing little details like a parking lot and a security booth, but many of the other elements outside the refinery are based on assets from other Maxis games. The streets and railroads are re-used from SimCity, but there’s also an entire barn from SimFarm sitting on the outskirts of the refinery. Jenny Martin served as an artist or art direction for all three of games, so it makes sense that she would repurpose the background graphics from other games to use in a low-budget prototype project that was never meant to be seen publicly.
Besides just reusing graphics, the Edit screen suggests that some features were copied directly from SimCity with a new coat of paint. Pipelines, in this case, seem to play the same role as power lines in SimCity, something to connect different structures together. This might tie into Will Wright’s comment in a lecture he gave at Stanford, when he complained that Chevron had expected SimRefinery would be as simple as taking SimCity and “plugging in a new set of graphics.” Maybe porting over features like power lines and railroad construction would have helped make the game more appealing to the higher-ups at Chevron who just wanted their own version of SimCity.
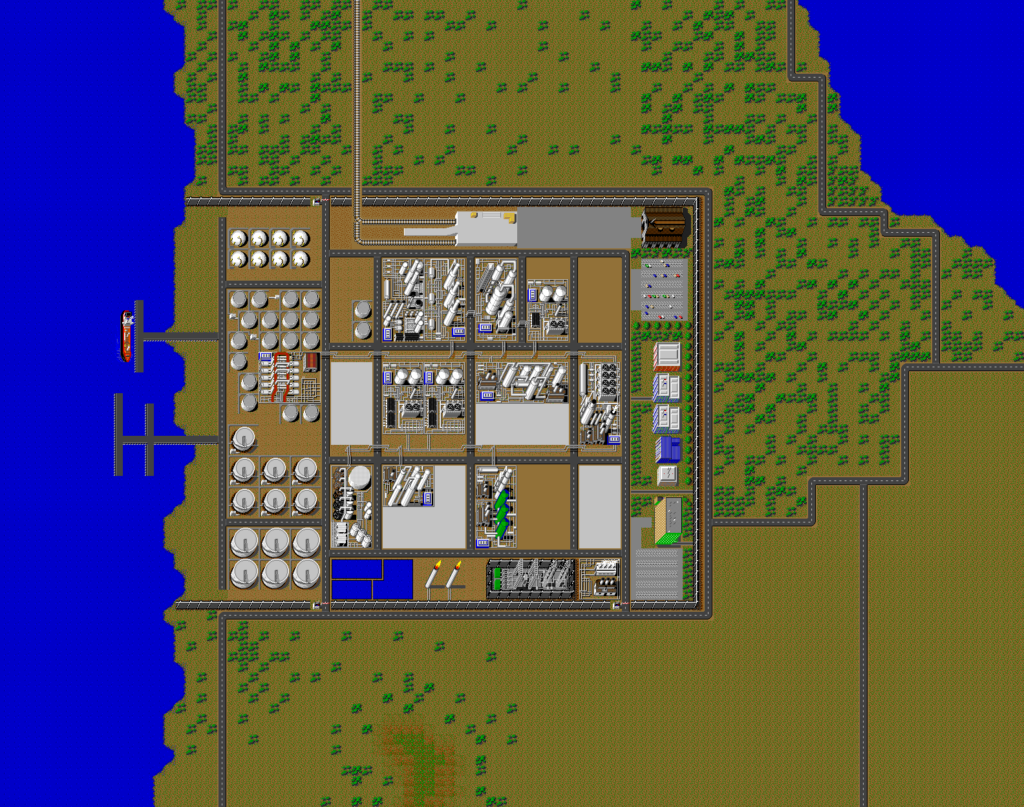
The full map of SimRefinery. Although the game was designed for and piloted at the Chevron Richmond Refinery, the SimRefinery Tour Book clarifies that it wasn’t meant to represent a specific refinery.
The bulk of SimRefinery is in the Map mode and the Unit window, where you can tinker with the plants at the refinery and alter the composition of the chemicals flowing between them. Honestly, as someone without a background in chemical engineering, it’s incomprehensibly dense to me. This is way above my understanding, and that’s incredibly interesting given the purpose of SimRefinery. The game was meant to help operators at the refinery better understand the relationships between their units, but it was also intended as a way for non-technical office staff at Chevron to see how the different departments at the refinery work together.
In its current state, I can’t imagine that SimRefinery would be easy for a layperson to understand on their own. The SimRefinery team was composed mostly of engineers, both at Maxis and Chevron, and the game absolutely feels like it was designed by engineers for engineers. There are help sections that briefly explain what each part of the refinery does, but that’s not enough to make sense of the wall of jargon and abbreviations.
The guides that came with SimRefinery would have been essential. In particular, the Tour Book gives a comprehensive walkthrough of the program, explaining much more than the in-game tutorial does. It uses simple, conversational language and seems to be geared towards first-time computer users, so they clearly expected that a non-technical audience would be playing this version. This is also probably where the training specialists at Chevron would make a difference, because someone from the finance office playing SimRefinery certainly would have needed guidance understanding this game. Chevron reported a positive response to SimRefinery from their internal testing, but perhaps MBS would’ve kept working on the user-friendliness of the game if it had gone into full development.
There are some hints in SimRefinery about what a more complete version of the game could have been like. The most intriguing feature is that you can design your own blend of gasoline. You can set the percentages of different components, then observe how switching production to this new blend will affect the relationships between different plants. That suggests something bigger in mind than just showing the office staff how the refinery works. It’s a feature that seems closer to what Maxis Business Simulations would later do with SimHealth – using the game as a test bed for experimenting with new ideas to see what impact they could have.
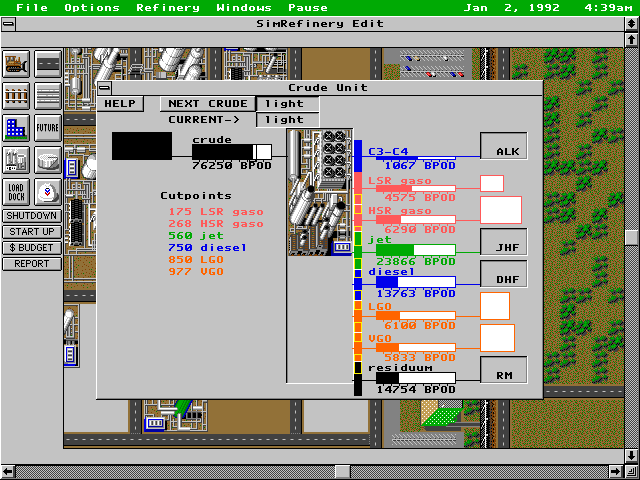
The functional parts of SimRefinery would be incomprehensible without a guide, a teacher, or a background in chemical engineering.
One of the most lurid details from the original article is that according to Bruce Skidmore, if you screwed things up badly, the refinery could explode. It looks like you can’t exactly set off an explosion in SimRefinery, but there’s plenty of oil fires and pollution. Instead of disasters like SimCity, SimRefinery has “external events,” a name that sounds like it was chosen by a stakeholder who was uncomfortable with the idea of “disasters.” There’s only a handful of events – a hot oil fire, a lightning strike, and a cloud of a non-toxic, abrasive substance that requires cleaning up. They don’t seem to be instigated by your actions though, and they play in a loop, each happening about once per day on the in-game clock.
It’s another placeholder feature in a game full of placeholders. This prototype is like a blueprint for what SimRefinery could have been if Chevron had decided to continue the project.
For people who wanted to play a full-fledged refinery simulation, it might be disappointing that the game is so unfinished. But what’s exciting is being able to see the specific way that it’s incomplete and what that tells us about the game’s development. In its prototype state, the core of SimRefinery is in place, but it’s rough. Many of the marquee features are incomplete, some graphics are borrowed from other games, and it’s very unapproachable. It seems like building a framework that Maxis Business Simulations could use for their projects was just as much a priority as making the actual refinery simulation.
Maxis Business Simulations was always working towards that next step – creating something that was fun as well as informative, that could bring together the best of their simulation design with the best of Maxis. SimRefinery was the first game, and it isn’t quite there, but it was, in a sense, a prototype for the company itself.
It’s still so surreal to see this game and see it out in the world now. At the end of tutorial in the SimRefinery Tour Book, there’s a page that I think is an appropriate way to end this part of the story:
The refinery is now in YOUR hands… Have fun!
I’ve had some experience working in downstream (refining and petrochemicals), so I hope that maybe I can provide some additional context for how a refinery engineering organization works.
Each unit within a refinery is like it’s own little business, with a CEO and a team of engineers behind them. The engineers are generally organized by trade, with some specializing in corrosion/pipes/heat exchangers/pressure vessels, others specializing in pumps/compressors and others still specializing in process engineering, which is the actual chemical engineering portion of the unit.
The degree of interconnectivity between the different units varies quite a bit depending on the kind of complex you have. In general, refineries tend to be hyper-interconnected, whereas other complexes, such as chemical plants tend to be much more independent.
The problem is that a refinery is a complicated beast, and understanding how they can work can take a decade of experience on the job. Most chemical engineering graduates wouldn’t be able to help you to understand this game. They would be able to help you with some basics, such as what vapor pressure is and how a distillation column works, but that’s really about it (broadly speaking).
If I were Chevron, (this is me theorizing here) the biggest benefit to a product like this is that it would allow me to train a young engineer on the bigger picture of how a refinery works. Many engineers, including myself, wouldn’t even begin to get familiar with the bigger picture of refinery operations until some sort of leadership or more senior role within the organization.
I’m not sure if this is something you’re familiar with or not, but I also know what the inspection tool was likely going to be implemented as. In a refinery, per internal and industry codes, there are inspection schedules that should be adhered to. Often these get pushed out for a number of reasons and theoretically if you didn’t inspect at all, you would begin to miss where wall thickness of critical equipment get below what is called a retirement limit – a critical thickness below which you cannot get below as the probability of failure (POF) rises to an unacceptable level. Eventually, you would gradually start to lose more and more material and then you would get below the pressure containing thickness. After getting to that point, you have a leak. Pretty much every piece of equipment in a refinery gets inspected and these inspection schedules are critical to ensure safe and reliable operations.
Thank you for sharing your perspective! This is an area I know basically nothing about, so it’s great to hear the practical angle on it.